本研究は競輪の補助を受けて実施しました |
表面テクスチャリングの最適化による
直接造形ABS/金属接合部材の高強度化・高信頼性化 |
研究の概要 |
|
樹脂積層造形技術は切削加工や鋳造など従来の加工法では製造できない複雑形状かつ高品質な製品の製造が可能となる技術であるが,反面,時間コストも含めた製造コストの課題が残る.また,樹脂そのものの強度の問題のため,構造材料として使用するためには金属部材との“マルチマテリアル化”が不可欠であるが,ボルト締結や接着技術を適用することはコスト低減や軽量化の妨げとなる.本申請課題で用いる直接造形樹脂/金属接合技術の特徴は,マルチマテリアルプロセスを造形プロセスと一体化することにより,コスト的な課題をクリアできる点である.金属と樹脂のマルチマテリアルプロセスについてはいくつか検討されているものの,三次元積層造形により樹脂を金属に直接造形接合した例は存在せず,申請者独自の技術である.また,一般には,工程を異にする表面テクスチャリングプロセスを製造プロセスと一体化する点は,これまでにない新規技術である.
この直接造形樹脂/金属接合技術を実機に適用するためには,長期使用を考慮して疲労と環境劣化に対する信頼性確保が不可欠である.そこで,直接造形ABS樹脂/Al合金接合体の疲労強度特性と環境劣化特性を定量的に評価する.そして,表面テクスチャリングの最適化により実用レベルの疲労強度特性・環境劣化特性を確保することを本申請課題の目的とする.
本提案技術は表面処理・接合・積層造形工程の一体加工工程で,マルチマテリアル製造の高効率化が期待され,自動車や飛行機などの運輸機器のみならずモバイル機器への展開などその工業的・経済的インパクトは大きなものである.さらに積層造形の長所である多品種・少量生産に適したプロセスである点も大きな長所である.加えて,IoT・AI対応が容易なロボットアームを用いたプロセスであることからオンライン遠隔制御も可能なプロセスである.生産人口の減少,高度技術の継承者不足の課題の解決も期待できる.さらに,with/postコロナ社会ではテレワークが推進されたが,加工工程の無人化が難しい第二次産業ではテレワークの導入が進んでいない.本提案技術はオンライン遠隔制御が可能なプロセスであり,現場の作業員の最小化と多くの技術者のテレワーク化の促進を可能とする技術で,postコロナ社会変革に大きな寄与が期待できる. |
研究の目的と背景 |
|
近年,構造部材の軽量化の目的から樹脂が積極的に活用されているが,耐熱性や強度特性の問題から,金属部材と複合して用いるマルチマテリアル化が必須となっている(1).
金属表面上へ樹脂を射出造形する二次加工が不要な技術に関する検討はいくつか行われているものの(2),3Dプリンタを用いた三次元造形により樹脂を金属に直接造形した例は少ない.
そこで本研究では,金属表面に樹脂を直接三次元造形する技術の確立を目的とし,静的引張試験,引張疲労試験,静的せん断試験,および,せん断疲労試験を実施することで,負荷モードの依存性を考慮した上で,樹脂/金属接合界面の異材接合界面強度を基準とした,積層造形プロセスの最適化について検討した.また,各試験から測定された機械的性質や,試験後の破断界面の観察結果などに基づき,ABS樹脂/Al合金異材接合体の接合メカニズム,および破壊メカニズムについて検討した.
|
得られた成果 |
|
接合に用いた樹脂は,3Dプリンタ用の純正ABS樹脂フィラメントである.造形に際し,あらかじめ24時間,80℃で真空乾燥処理を施した.一方,金属基材にはAl合金板(20mm×20mm×厚さ3mm)を用いた.基材表面を異なる条件でレーザ粗面化処理することにより,構造サイズの異なる微細孔を有する3
種類の表面性状のAl基材を準備した.図1に基材表面状態を示す.いずれも金属表面から内部に微細な孔が広がる複雑な粗面構造を形成している.本研究では,各供試材の微細孔が小さい方からFine材,Middle材,
Coarse材と呼び,それぞれの算術平均粗さPaは10.59µm,18.43µm,23.27µmであった.
本研究では,市販の3Dプリンタを用いてAl合金基材へのABS樹脂の直接造形を行うことで,直接造形樹脂/金属異材接合体を作成した.3Dプリンタ内にセラミックヒーターを設置し,ヒーター上面にAl基材を固定し積層造形を行うことで,積層時の基材温度を一定に保っている.本研究で用いる,まず.積層形状の安定化,および,接合性の改善を可能にするものとして,本研究において最適な造形プロセス条件を選定した.この最適プロセス条件にて3種類の表面性状のAl合金基材上に円柱形状の樹脂片を直接積層造形した.
静的引張試験から得られた,金属表面性状ごとの静的界面強度を図2に示す.直接造形樹脂/金属異材接合体の実験結果については,いずれも4回の試験で得られた結果の平均値を静的強度として示し,そのばらつきの範囲をエラーバーで表記した.図2より,静的引張強度は金属基材表面状態に依存して変化し,Middle材で20MPa程度と最も高い接合界面強度を示した.この結果は樹脂単体造形材試験片,および,接着剤を用いてABS樹脂積層造形体をMiddle材に接着した試験片の静的引張強度よりも高い値であった.これらの結果より,直接造形樹脂/金属接合体の界面強度は十分な強度以上を有していると言えよう.なお,本研究室のこれまでの実施試験である単層におけるせん断強度の評価結果においても,本研究の結果と相違なくMiddle材試験片で最も高い値を示していた.
直接造形樹脂/金属異材接合体,および,樹脂単体造形試験片を対象として実施した引張疲労試験の結果を図3に示す.引張疲労強度においても静的強度と同様に,Middle材条件で約2.2MPaと最も高い値となった.ただし,この結果は静的引張強度の1/8以下であり,一般的な金属材料ではその疲労限度は引張強度の2/3であることを鑑みると,きわめて低い疲労強度しか得られなかった.この要因として,ABS樹脂部分の積層造形時に生じる各層間の微小な空隙(層間弱部)の存在が影響しており,繰り返し疲労負荷を受けた際,これらの弱部から疲労き裂が発生・進展したため,顕著に疲労強度が下がったものと考えられる.
Middle材を用いた引張疲労試験,および,せん断疲労試験から得られた,荷重モードごとのS-N曲線を図4に示す.図より,Middle材条件のせん断疲労強度は約2.6MPa程度であり,この値は引張疲労強度と比較すると18%程度高い値となった.この結果より,直接造形樹脂/金属異材接合体の界面疲労強度に及ぼす荷重モードの依存性が存在すると言える.これは,層間弱部が基材表面粗さの形状に沿って正弦曲線上に続いていることに起因し,せん断負荷においてはAl基材の凹凸形状がき裂進展抵抗として働くことで層間弱部以外にもき裂が進展しやすいためと考えられる.
|
|
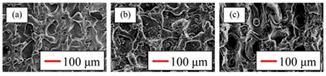
図1 Surface morphologies of Al-alloy after laser
processing ; (a) Fine structure, (b) Middle
structure, (c) Coarse structure
図2 Comparison
of static bonding strength between effect of
metal surface roughness and molding method
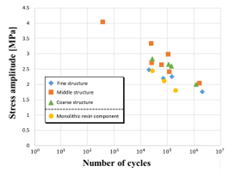
図3 Comparison of fatigue bonding strength between effect of metal surface
roughness and molding method
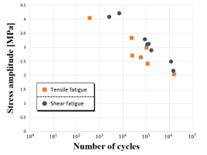
図4 Effect of loading mode on fatigue bonding strength in Middle structure
|
|
|
|
|
|