本研究は競輪の補助を受けて実施しました |
非破壊評価した粘弾塑性特性に基づく
樹脂系構造材料の高精度破損寿命予測技術の開発 |
研究の概要 |
|
樹脂材料の粘弾性特性を簡易に評価できる技術を確立した.さらに,樹脂材料の低サイクル疲労試験を実施し,疲労寿命を整理するパラメータを検討した.その結果,球状圧子押し込み試験と有限要素法を用いた逆解析により評価した粘弾性特性を考慮した応力振幅をパラメータと用いることにより樹脂材料の疲労寿命が良好に整理できることを明らかにした.さらに,得られた結果に基づき疲労寿命予測手法を検討し,従来の金属材料の低サイクル疲労寿命予測手法を適用した場合に比較して極めて高い予測精度で寿命が予測できる技術を開発した. |
研究の目的と背景 |
|
環境負荷低減と燃料コスト削減の目的から,輸送機器構造材料への樹脂系材料の適用が求められている.しかし,耐久性の保証が難しいため,輸送機器構造材料への適用が制限されてきた.これは,鉄鋼に代表される金属材料に比べて,樹脂系材料の力学特性が製造条件に過敏でロット間差が大きく,さらに,温度・湿度や紫外線などの環境負荷に影響を受けて力学特性が大きく変化するため,樹脂系材料の破損寿命を予測することが困難であること起因している.そこで,樹脂系構造部材の粘弾塑性特性を非破壊で簡易評価し,粘弾性特性を考慮した疲労寿命予測する技術について検討した.
|
得られた成果 |
|
開発した計装化押し込みシステム(図1)による球状圧子押し込み試験と,3並列マクスウェルモデルによる逆解析(図2)を実施し,粘弾性特性を評価した.実験と解析で得られた代表的な押し込み荷重曲線を比較して図3に示す.図3より, 3並列マクスウェルモデルでは負荷中と保持開始時の挙動を高精度に再現できている.球状圧子押し込み試験と逆解析を用いて,粘弾性特性として緩和剛性率Giを評価した.結果を図4に示す.図4より,緩和剛性率Giの割合は材料や環境試験の影響を受けて変化している.
曲げ疲労試験装置1号機,2号機(図5)と3号機として環境試験機内疲労試験装置(図6)を試作した.試作した曲げ疲労試験装置を用いて低サイクル疲労試験を実施した.低サイクル試験中の代表的な応力-ひずみ関係をおいて,従来の金属材料に認められるヒステリシスループとは形状が異なる,樹脂材料特有のヒステリシスループを呈していた.すなわち,負荷時にある程度ひずみが大きくなると変形抵抗が増加し,除荷時には急激に応力が減少した曲線(すなわち,引張除荷の際は下に凸,圧縮除荷の際は上に凸の曲線)を呈していた.また,応力がゼロにおいてひずみが残存し,非弾性ひずみ範囲Δεinが生じていた.ただし,試験を中断した場合,直ちにひずみが減少し,応力-ひずみ関係が原点に戻ったことから,ヒステリシスループに認められる非弾性ひずみ範囲Δεinは,一般的な金属で主成分となる塑性ひずみ成分はほとんどなく,ほとんどが粘性成分と考えられる.
以上の検討結果に基づき,応力振幅σaを緩和剛性率G3で基準化したσa/G3をパラメータとして疲労寿命Nf を整理した結果を図7に示す.図より,σa/G3により,材料や環境試験の影響にかかわらず全ての試験片の疲労寿命Nf
を統一的に整理できている.緩和剛性率で基準化した応力振幅σa/G3をパラメータとして疲労寿命を予測し,予測値と実験結果を比較した結果を図8に示す.緩和剛性率で基準化した応力振幅σa/G3を用いることにより高精度に疲労寿命を予測できている.
緩和剛性率で基準化した応力振幅σa/G3をパラメータとして疲労寿命を予測した際の実験値からの相違について,金属材料に対して一般的に適用されるひずみ振幅εa,応力振幅σaの結果も含めて図9に示す.ひずみ振幅εaをパラメータとしたとき環境試験により大きな相違が,応力振幅σaをパラメータとしたときは材料が異なるとき大きな相違が生じ,どちらも多くのデータが予測精度20%を満たしていない.対して,緩和剛性率で基準化した応力振幅σa/G3がパラメータ用いることにより,環境の影響を受けた場合30%程度の予測精度であったものの,20%の予測精度でほぼ低サイクル疲労寿命を予測できた.
|
|
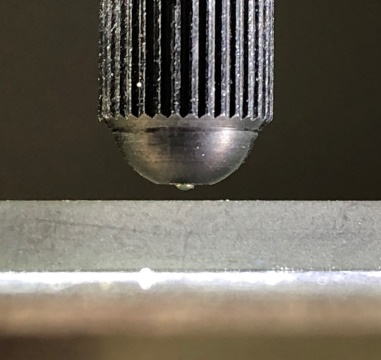
(a) 外観 (b) 圧子押し込み部拡大
図1 球状圧子押し込み装置
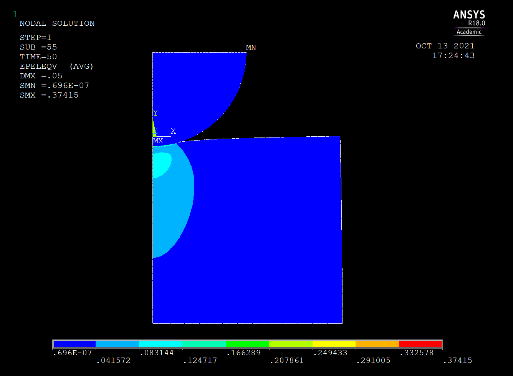
図2 解析結果(ひずみ分布)の例
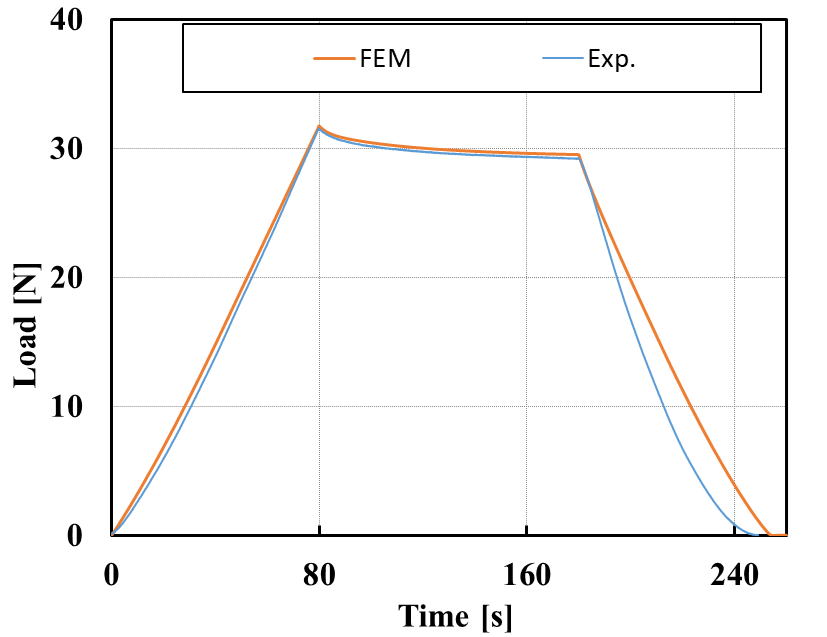
図3 球状圧子押し込み試験結果
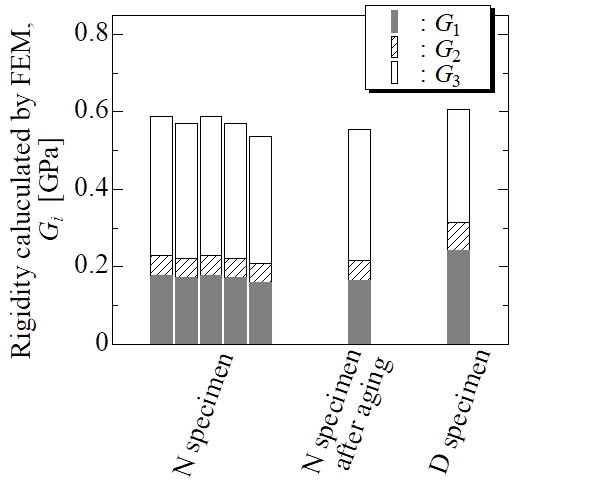
図4 緩和剛性率Gi
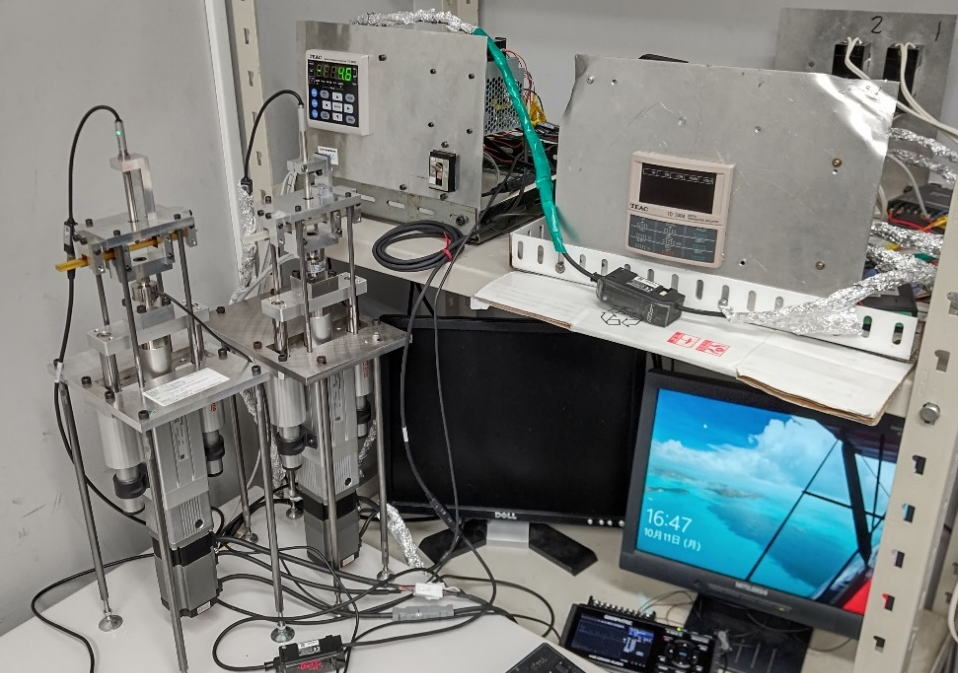
図5 疲労試験装置(1号機(右)と2号機(左))
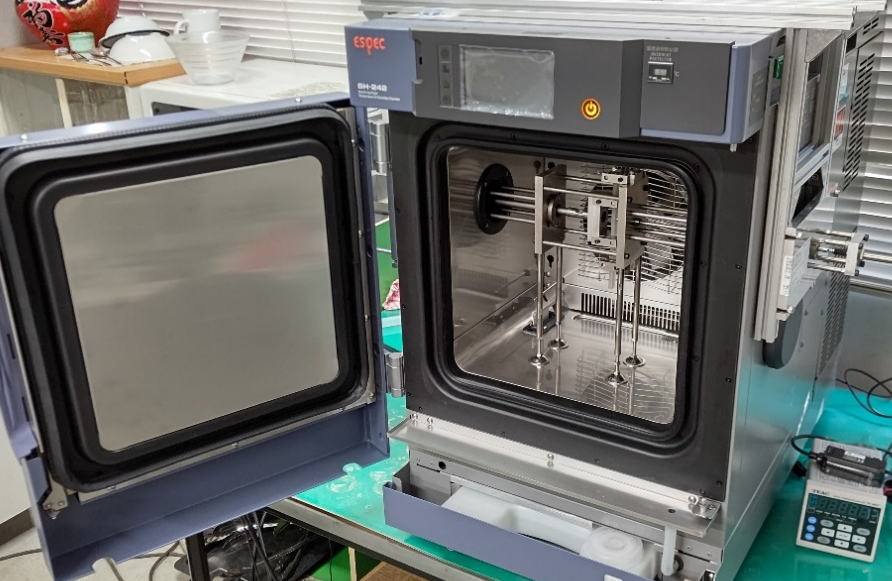
図6 疲労試験装置(3号機)
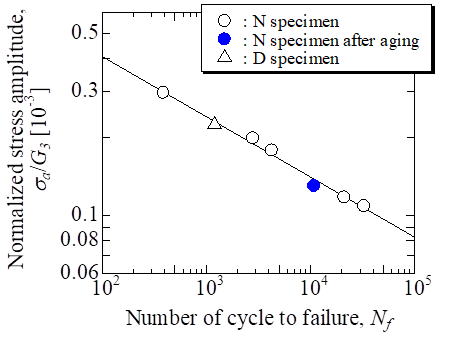
図7 疲労寿命Nf 整理結果
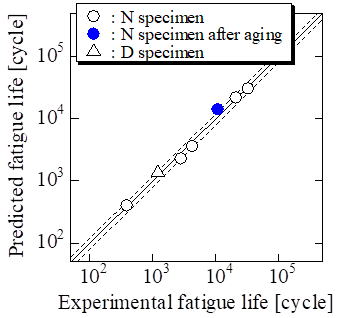
図8 寿命予測結果
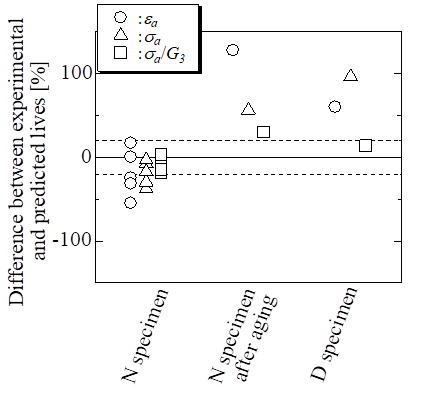
図9 各パラメータの寿命予測精度の比較
|
|
|
|
|
|